Membranlar, seçici bir şekilde ayırmanın ve taşınmanın gerçekleştiği yarı geçirgen bariyerler yani bileşenleri yapı ve boyutlarına göre ayıran bir ara faz olarak tanımlanabilir. Bu bariyerler katı, sıvı ya da gaz halinde olabilirler. Membran proseslerinde ayırma işlemi membranın hem kimyasal hem de fiziksel özellikleriyle belirlenmekte ve basınç farkı, konsantrasyon (kimyasal potansiyel) farkı, elektriksel potansiyel farkı ve sıcaklık farkının biri veya birleşimleriyle oluşturulan itici kuvvet ile gerçekleşmektedir.
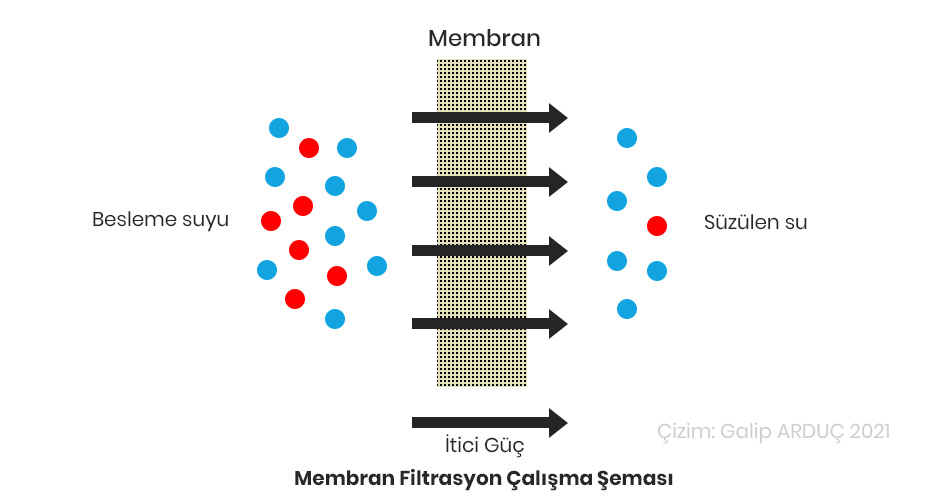
Membran prosesleri, damıtma gibi geleneksel ayırma prosesleriyle yarışabilen ve genellikle düşük enerji avantajı sunan ayırma prosesleridir. Bir membranda taşınım hızı membran kalınlığıyla ters orantılı olup ekonomik nedenlerden dolayı yüksek taşınım hızı istendiği için membran mümkün olduğunca ince olmalıdır. Alt destek yapısı ve yüzey katmanı, tek bir işlemle veya ayrı olarak da gerçekleştirilebilmektedir. Ayırma özellikleri ve geçirgenlik hızları yüzey tabakasında belirlenip alt tabaka mekanik destek işlevi görmektedir (Leboda ve Mendyk 1991). Knudsen difüzyonu ve yüzey difüzyonu, gözenekli membran aracılığıyla gaz ayırımının önemli mekanizmalarıdır. Knudsen difüzyonu, gaz molekülünün kat ettiği ortalama serbest yol, gözenek çapından yeteri kadar büyük olduğunda, geçen gaz molekülleri arasındaki çarpışma da yeterli seviyeye ulaştığında oluşur. Gözenek boyutu, geçen gaz molekülleri kadar küçüldüğünde yüzey difüzyonu önem kazanmaktadır.
Membranlar üç büyük gruptan oluşurlar; biyolojik, organik (polimerik) ve inorganik membranlar. İnorganik membranlar kendi içinde seramik ve metalik membranlar olarak iki grupta sınıflandırılırlar. Gözenek büyüklüğüne (ya da membrandan geçen parçacıkların büyüklüğüne) göre hem organik hem de inorganik membranlar, mikrofiltrasyon (MF), ultrafiltrasyon (UF), nanofiltrasyon (NF), ters osmos (RO) ve gaz ayırım membranları olarak ayrılabilirler. Su arıtma işlemleri, birkaç tip membran kullanılarak gerçekleştirilir. Bu membran türleri, mikrofiltrasyon (MF), ultrafiltrasyon (UF), ters osmoz (RO) ve nanofiltrasyon (NF) membranlarını içerir.
MF membranları en büyük gözenek boyutuna sahip olup tipik olarak büyük bileşenleri ve çeşitli mikroorganizmaları reddetmektedir. UF membranları, MF membranlarından daha küçük gözeneklere sahiptir ve bu sebepten dolayı, büyük parçacıklar ve mikroorganizmalara ek olarak, proteinler gibi çözünür makromolekülleri ve bakterileri de reddedebilirler. Ters osmoz membranları gözeneksizdir ve bu nedenle, parçacıkları ve hatta tuz iyonları, organik maddeler, vs. gibi çok düşük molar kütle türlerini hariç tutar. NF membranları, diğerlerine kıyasla yenidir ve bazen “gevşek” RO membranları olarak adlandırılır. Gözenekli membranlardır, ancak gözenekler 10 Å (on angström) veya daha az düzende oldukları için, RO ve UF membranları arasında performans gösterirler (Baker 2004).
Membranların Avantaj ve Dezavantajları
Membranların avantajları aşağıda maddeler halinde verilmiştir;
- Membran sistemleri genellikle bir faz değişimine ihtiyaç duymazlar (pervaporasyon hariç). Bu nedenle, enerji gereksinimleri (enerji tüketimleri) düşüktür.
- Neredeyse tüm işlemler oda sıcaklığında (düşük sıcaklıkta) devam eder, bu nedenle yüksek sıcaklıklara dirençli olmayan bileşiklerle başa çıkabilirler.
- Hem konsantre hem de permeat (süzüntü) akımları geri dönüştürülerek kullanılabilirler.
- Suyun geri kazanılması için uygulandığında, büyük su hacimlerinin taşınmasını engellerler ve kanalizasyon tesislerinde Kimyasal Oksijen İhtiyacı (COD) yüklenmesinin azaltılmasını sağlarlar.
- Ayırmaya ihtiyaç duyulan birçok işlem, membran prosesleriyle gerçekleştirilebilir. Bunun nedeni ise membranların, parçacıkların görülebileceği bir ölçekte ve moleküler boyutta ayırma yapabilmesidir.
- Membran prosesleri, basit bir akım şemasına sahiptir ve işletme kontrolleri karmaşık değildir. Ayrıca yardımcı bir ekipmana ihtiyaç duymazlar. Bundan dolayı, basit, doğrudan işletme, düşük bakım onarım seçeneği sunabilirler.
- Bileşenlerin ayrılması işleminde kullanılan membranlar, oldukça yüksek seçiciliklerle elde edilebilirler. Bu seçicilik değerleri ise, distilasyon işlemleri için gerekli olan bağıl uçuculuk değerlerinden daha fazladır.
- Çok sayıda inorganik ve polimer malzemeden elde edilebilirler. Böylece geniş aralıkta bileşenlerin ayrılmasına olanak sağlarlar.
- Membran işletmelerinde, basit ve çevreye zararı olmayan maddeler kullanıldığından çevre için potansiyel olarak daha iyidir (Nũnes ve Peinemann 2001).
- Membran proseslerinde belirli bir boyut sınırlandırması yoktur, modüler olarak tasarımı yapılabilir, taşınabilir ve herhangi bir inşaat gerektirmezler. Ayrıca düşük alan ihtiyacına sahiptirler
Ancak bu avantajlarının yanısıra dezavantajları da membranların daha yaygın kullanımını sınırlamaktadır.
Dezavantajları aşağıda sıralanmıştır; Membran prosesleri, damıtma gibi ayırma işlemleriyle karşılaştırıldığında kolayca gerçekleştirilemezler. Genellikle bir aşama içerirler, ancak bazen iki veya üç aşamaya sahip olabilirler ve bu nedenle ayrılacak membranın daha fazla seçiciliğe sahip olması gerekir. Genellikle işlemler, düşük seçicilik/daha fazla aşama yerine yüksek seçicilik/birkaç aşama şeklinde yapılır. Ancak aşama sayısı arttıkça seçicilik azalır. Membran modülleri, çoğu membranın polimer bazlı olması ve polimerlerin bütünlüklerini, 100 ºC’nin üzerindeki sıcaklıklarda tutamaması nedeniyle, membran proseslerinin bazen kimyasal işlem koşulları ile uyumlu olmadığı anlamına geldiğinden, genellikle oda sıcaklığının çok üzerindeki sıcaklıklarda çalışamazlar.
Membran prosesleri paralel olarak membran modülleri içerir ve daha yüksek besleme hızlarının sürmesi için çoğaltılmalıdır. Membran ayırma işlemlerinde nadiren iki saf ürün üretimi vardır. İki akıştan biri genellikle diğer az miktarlı bileşenler tarafından kirletilir. Ozmotik basıncın neden olduğu sorunlar nedeniyle, bir ürün sadece bir kalıntı (retentate) gibi konsantre olabilir. Diğer durumlarda, süzüntü (permeat) akımı, kalıntıda konsantre olmaya çalışan önemli miktarda bileşen içerebilir, çünkü membranın seçiciliği sonsuz değildir. Sonunda, bazı besleme akışları işlenirken, membran ayırmalarında önemli miktarda kirlenme problemi ile karşılaşılabilir. Bu kirlenme, membranların içinden geçirilme hızını engelleyebilir, performansı düşürebilir ve bu tür uygulamalar için uyumsuz kılabilir(Baker 2004).
Membranların Uygulama Alanları
Membranlar, kimyasal teknolojide önemli bir yer edinmiş ve geniş bir uygulama yelpazesinde giderek daha fazla kullanılmaktadır. Membranın her uygulamada yararlanılan temel özelliği, onunla temas eden kimyasal türlerin nüfuz etmesini kontrol etme yeteneğidir. Ambalajlama uygulamalarındaki amaç, genellikle nüfuzu (geçişi)tamamen önlemektir. Kontrollü ilaç salım uygulamalarında amaç, bir ilacın rezervuardan vücuda nüfuz oranını azaltmaktır. Ayırma uygulamalarındaki amaç ise, membranın karışımdaki bir bileşenin, serbestçe nüfuz etmesine izin verirken, diğer bileşenlerin geçişini engellemektir (Bruschke 1995).
Membran prosesleri, ürünlerin geliştirilmesi, değerli bileşenlerin geri kazandırılması, karışımın kararlı hale getirilmesi, çözeltilerin estetiğinin arttırılması ve proseslerin ekonomisine katkıda bulunulması gibi kullanım alanlarının olduğu çok çeşitli uygulamalarda bulunmuştur. Mikrofiltrasyon, ultrafiltrasyon, ters ozmoz ve nanofiltrasyon işlemlerinden her biri, kullanımlarında büyümeye devam edecek endüstriyel uygulamalar için farklı ayırma seçenekleri sunar. Sürdürülebilir bir endüstriyel büyüme için süreç yoğunlaştırma stratejisini izleyen yenilikçi süreçlerin geliştirilmesi, kirletici olmayan, hatasız ve güvenli endüstriyel proseslerle üretim için kritik öneme sahiptir. Membran işlemleri, geleneksel ayırma ve reaksiyon işlemlerine kıyasla daha yüksek verimlilik göstermektedir.
Yenilikçi üretim döngülerinin rasyonelleştirilmesi için yeni seçenekler sunarlar. Membran mühendisliği, su tuzunun giderilmesinde (desalinasyon), belediye suyunun tekrar kullanılmasında, petrokimyasallarda ve gaz ayırım alanında önemli bir rol oynamaktadır.
Ters osmoz (RO), mikrofiltrasyon (MF), ultrafiltrasyon (UF) ve nanofiltrasyon (NF), elektrodiyaliz, pervaporasyon, vb. gibi geleneksel membran ayırma işlemleri büyük ölçüde birçok farklı uygulamada kullanılmaktadır. Membranlar, belediye tesislerinde içme suyu ve deniz suyunun tuzdan arındırılması işlemleri sayesinde iyi bilinmektedir.
Bununla birlikte, takdir edilmeyen şey, dünyadaki endüstriyel uygulamalarda membran teknolojisinin ne kadar çok kullanıldığıdır. Membranlar, faz değişimi olmaksızın ve ısı uygulanmadan ayırma gerçekleştirerek bazı uygulamalar için avantajlı olabilirler. Zaman zaman membran tesisi bir belediye tesisine kıyasla büyük olmayabilir, ancak sistemin ve sürecin değeri genel ekonomik uygulanabilirlik için kritik öneme sahip olabilir.
Bazen, bir endüstriyel tesiste mevcut olan su, uygulamanın ihtiyaçlarını karşılamayabilir ve böylece işlemin yürütülebilmesi için kalitenin iyileştirilmesine yönelik olarak membranlar kullanılabilir. Belki de proseslerden boşalma işlemi çok fazladır ve membranlar tarafından kolaylaştırılabilen bir azaltma aşamasına ihtiyaç vardır. Bazen, çözeltinin derişimi istenen seviyede olmayabilir ve konsantrasyonu ayarlamak için kolay ve etkili bir yol olarak membranlar kullanılabilir. Ayrıca membranlar, membran biyoreaktörlerinde, yiyecek ve süt ürünleri, farmasötik ve diğer tesislerde atık arıtımı için kullanılır.
Uygulama alanları;
Gıda ve içecek alanında;
- Şişelenmiş Su
- Bira, şarap ve alkollü içecekler
- Meyve suları ve akçaağaç şurubu
- Süt ve peynir
Endüstriyel alanda;
- Biyokimyasal proseslerin arıtılması
- Petrol rafinerisi
- Boya, yapıştırıcı ve solvent geri kazanımı
- Yarı iletken, kazan besleme ve enerji endüstrisi ihtiyaçları gibi yüksek saflıkta uygulamalar.
Madencilik ve metal proseslerinde;
- Kaplama işlemleri ve atıkların azaltılması
- Altın ve uranyum geri kazanımı
- Değerli metallerin geri kazanımı
- Depolama sahası sızıntı suyunun azaltılmasını içermektedir.
Membran prosesleri, suyun nüfuz etmesine veya içinden geçmesine izin veren ancak diğer bileşenlerin bu süzüntüyle birlikte gitmesini reddeden veya geciktiren bir bariyer tabakası kullanır. Mikrofiltrasyon ve ultrafiltrasyon durumunda, polimerdeki farklı gözenekler suyun bariyer boyunca akmasına izin verir, ancak gözeneklerden daha büyük türlerin geçişini geciktirir/reddeder. Ters ozmoz bariyer katmanları farklı gözeneklere sahip değildir, ancak suyun bariyer katmanından yayılmasına izin verirken karışımdaki çözünmüş iyonların çoğunu reddeder.
Isı, ayırma işlemini etkilemek için kullanılmadığından, karışımdaki bileşenlerin termal bozulmaya maruz kalma olasılığı daha düşüktür. Membranlar, diyatomik toprak filtrasyonu (DE), santrifüj, ekstraksiyon, döner vakum filtreleri, buharlaştırma, damıtma ve ürün eldesinde kullanılan diğer ünite işlemlerinin yerini almaktadır. İçeceklerin, ilaçların ve sütün soğuk sterilizasyonu, membran sistemlerinden yararlanır. Ticari olarak temin edilebilen membran ürünlerinin çoğu, polimerik bir bariyer katmanına sahiptir, ancak farklı gözeneklere sahip seramik membranlar, zorlu koşullarda kullanılmıştır ve yeni uygulamalarda kullanım alanı bulmaktadır. Seramik membranların, mikrofiltrasyon ve ultrafiltrasyon filtreleri olarak sınıflandırdığı gözenek boyutları vardır.
Membranların Sınıflandırılması
Temelde, bir membran, kendisi ile temas eden kimyasal bileşenlerin geçirgenliğini düzenleyen, ayıran, ince bir ara yüzeye sahiptir. Bu yarı geçirgen ara yüzey moleküler olarak homojen olabilir, yani bileşim ve yapı bakımından tamamen tek tip olabilir veya örneğin sonlu boyutlu delikler veya gözenekler içeren kimyasal veya fiziksel olarak heterojen olabilir. Bununla birlikte, membran yapısı nötr veya elektriksel yüklere sahip olabilir. Membranlar çok sayıda birbirinden farklı malzemeden üretilebilirler.
Üretildikleri malzemeye bağlı olarak ise biyolojik ve sentetik membranlar olarak iki gruba ayrılabilirler. Organik (polimerik) ve inorganik (seramik, metalik) membranlar ise sentetik membran grubuna girerler.
Farklı bir sınıflandırma ise mikrofiltrasyon ve ultrafiltrasyon işlemlerinde kullanılan açık ve gözenekli membranlar ile gaz ayırma ve pervaporasyon proseslerinde kullanılan yoğun, gözeneksiz membranlar arasında yapılabilir. Gözenekli membranlar için, ayırma özelliğini belirleyen malzeme seçimi değil gözenek büyüklüğü, parçacık veya moleküler büyüklüğüne bağlı gözenek boyutu dağılımıdır (Nũnes ve Peinemann 2001). Membranlar ayrıca gözenek boyutlarına göre de sınıflandırılabilirler. IUPAC tarafından önerilen gözenek boyut sınıflandırması makro, mezo ve mikro gözenekli membranlar şeklindedir.
Ayrıca mikro gözenek ve dar bir mezo gözenek aralığı için nano gözenek terimi de kullanılmaktadır. Kesin bir tanım verilmeden nano gözenek boyut aralığının üst sınırı esas olarak mikro gözenek boyutuyla ilgili olduğundan 2-3 nm olarak belirlenmiştir. Boyutları çizelge 2.1’de verilmiştir.
Çizelge 2.1 Gözenek Boyutlarına Göre Membranlar
Membran | Gözenek Boyutu (nm) | Uygulama Alanı |
Makrogözenek | ˃ 50 | UF, MF ve filtrasyon |
Mezogözenek | 2-50 aralığında | UF, NF |
Mikrogözenek | ˂ 2 | NF |
Süpermikrogözenek | 0,7-2 | RO, NF |
Ultramikrogözenek | ˂ 0,7 | RO, GS, dializ |
Ultragözenek | ˂ 0,35 | RO1, GS2, dializ |
Başlıca membran türleri maddeler halinde verilmiştir:
İzotropik mikrogözenekli membranlar
Mikrogözenekli bir membran, geleneksel ayırmalarda kullanılan bir filtreye yapı ve işlev olarak çok benzemektedir. Rasgele dağılmış, birbirine bağlı gözenekli, sıkı ve yüksek oranda boşluklu bir yapıya sahiptir.
Bununla birlikte, bu gözenekler, geleneksel bir filtrede bulunanlardan çok küçük olmaları (0,01-10 mm çapında) nedeniyle farklılık gösterir. En büyük gözeneklerden daha büyük olan tüm parçacıklar membran tarafından tamamen reddedilir. En büyük gözeneklerden daha küçük, fakat en küçük gözeneklerden daha büyük olan parçacıklar, membranın gözenek büyüklüğü dağılımına göre kısmen reddedilir. En küçük gözeneklerden çok daha küçük parçacıklar membrandan geçer. Bu nedenle çözünenlerin mikro gözenekli membranlarla ayrılması, temel olarak moleküler boyut ve gözenek boyut dağılımının bir fonksiyonudur. Genel olarak, sadece büyüklük olarak farklılık gösteren moleküller, örneğin ultra filtrasyon ve mikro filtrasyonda, mikro gözenekli membranlarla etkili bir şekilde ayrılabilir.
Gözeneksiz yoğun membranlar
Gözenekli olmayan yoğun membranlar, membrandan geçebilen bileşenlerin basınç, konsantrasyon veya elektriksel potansiyel farkı itici gücü altında difüzyonla taşındığı yoğun bir filmden oluşur. Bir çözeltinin çeşitli bileşenlerinin ayrılması, membran içindeki difüzivite ve çözünürlükleri ile belirlenen taşıma hızlarıyla doğrudan ilgilidir.
Gözenekli olmayan, yoğun membranların önemli bir özelliği, konsantrasyonları (yani, çözünürlükleri) önemli ölçüde farklılık gösteren ancak benzer büyüklükteki bileşenlerin dahi membran içinden geçerek ayrılabilmesidir. Çoğu gaz ayırım, pervaporasyon ve ters ozmoz membranları, ayırma işlemini gerçekleştirmek için yoğun membranlar kullanır.
Bununla birlikte, bu membranlar, akıyı geliştirmek için genellikle asimetrik bir yapıya sahiptir. Organik (polimerler) ve inorganik (metaller) olmak üzere çok sayıda farklı malzemeden hazırlanabilirler. Yoğun inorganik membranlardan metalik membranlara, başlıca hidrojen ayırımında kullanılan paladyum alaşımlı membranlar örnek olarak verilebilir (Bazzarelli vd. 2015).
Elektrik yüklü membranlar
Elektrik yüklü membranlar, yoğun veya mikro gözenekli olabilir, ancak en çok gözenek duvarları pozitif veya negatif yüklü iyonları sabit olarak taşıyan mikro gözenekli yapıdadır. Pozitif yüklü iyonlara sahip bir membran, bir anyon değişim membranı olarak adlandırılır, çünkü çevresindeki akışkanda bulunan anyonları bağlar. Benzer şekilde, negatif yüklü iyonları içeren bir membran, bir katyon değişim membranı olarak adlandırılır. Yüklü membranlarla ayırma işlemi, temelde, membran yapısının sabit iyonları ile aynı yükteki iyonların dışlanması ile gerçekleşir. Ayırma işlemi, solüsyondaki iyonların derişim ve yükünden etkilenir. Örneğin, monovalent iyonlar iki değerli iyonlardan daha az etkili bir şekilde hariç tutulur ve yüksek iyonik kuvvetli çözeltilerde seçicilik azalır. Elektrik yüklü membranlar, elektrolizde elektrolit çözeltileri işlemek için kullanılır.
Asimetrik membranlar
Membrandan geçen türlerin taşınım hızı, membran kalınlığıyla ters orantılıdır. Membran ayırım işlemlerinde ekonomik nedenlerden dolayı yüksek taşınım hızı istendiği için membran mümkün olduğunca ince olmalıdır. Geleneksel film üretim teknolojisi, mekanik olarak güçlü, hatasız film üretimini yaklaşık 20 µm kalınlığa kadar sınırlar. Asimetrik membran yapıları elde etmek için yeni membran üretim tekniklerinin geliştirilmesi, son 30 yıl boyunca membran teknolojisinin atılımlarından biriydi. Asimetrik membranlar, çok daha kalın, gözenekli, yoğun bir alt yapı üzerinde desteklenen oldukça ince bir yüzey katmanından oluşur. Yüzey katmanı ve destek yapısı tek bir işlemle veya ayrı olarak oluşturulabilir. Membranın ayırma özellikleri ve geçirgenlik oranları sadece yüzey tabakası tarafından belirlenir; altyapı mekanik bir destek işlevi görür. Asimetrik membranların sağladığı yüksek akıların avantajları çok fazladır, bu yüzden neredeyse tüm ticari prosesler bu tür membranları kullanırlar (Baker 2004).
Seramik, metal ve sıvı membranlar
Membran malzemelerinin organik polimerler olduğu ve aslında ticari olarak kullanılan membranların büyük çoğunluğunun polimer bazlı olduğu uzun süredir tartışma konusudur. Mikro gözenekli membranların özel bir sınıfı olan seramik membranlar, çözücü direnci ve termal kararlılığın gerekli olduğu ultrafiltrasyon ve mikrofiltrasyon uygulamalarında kullanılmaktadır. Yoğun metal membranları, özellikle paladyum membranları, hidrojenin gaz karışımlarından ayrılması işlemi için göz önünde bulundurulmaktadır. Birleştirilmiş ve kolaylaştırılmış taşıma işlemleri için desteklenmiş veya emülsiyon haline getirilmiş sıvı membranlar geliştirilmektedir.
Membranın kullanım ömrü, ayırma ve seçicilik özelliği, işletme koşulları, membran maliyetleri ve verimlilik özellikleri, membran proseslerinde kullanılan membran tipi seçiminde dikkate alınan parametrelerdir.
İnorganik membranlar
norganik membranlar seramik, karbon, silika, zeolit, çeşitli oksitler (alüminyum, titanyum, zirkonyum) ve palladyum, gümüş ve alaşımları gibi metallerden üretilmiş membranlardır. Zor koşullar altında çalışabilirler ve spesifik moleküller için oldukça seçici ve geçirgen olabilirler. İnorganik membranlar, yeterince geçirgen olmaları durumunda bağımsız tabakalar ve tüpler olarak yapılır. Durum böyle değilse, çok katmanlı destek yapılarında ince film olarak yapılır. Destekleyici yapılar yeterince güçlü ve geçirgen olmalıdır. Membran için pürüzsüz bir yüzey oluşturmak için gözeneklilikte yavaş yavaş veya kademeli değişikliklere ihtiyaç vardır. Önemli uygulamalara örnek olarak;
- Kömür kökenli gazdan H2 ayrımı
- Doğal gaz ve kömür santrali baca gazından CO2 ayrımı
- Etkili yanma ve petrokimyasal uygulamalarda kullanmak için O2’nin havadan ayrılması
- Kimyasal reaksiyon karışımlarından H2O’nun ayrılması
- Çözünmüş tuzların ve diğer kirletici maddelerin sudan çıkarılması verilebilir (Verweij2012).
İnorganik membranlar mikro gözenekli veya gözeneksiz (yoğun) olabilirler. Mikro gözenekli inorganik membranlar amorf ve kristal seramik membranları içermektedir.
Yoğun inorganik membranlar, polikristal seramik veya metalden elde edilirler. Mikro gözenekli membranlar daima, gözenekli bir inorganik destek üzerine desteklenecek bir film olarak hazırlanırlar. Bazı yoğun metalik membranlar da bu şekilde hazırlanabilirler.
Bunlar 300-1000 ºC gibi yüksek sıcaklık aralıklarında işletilebilirler. Bu membranlar ayrıca kimyasal ayrışmaya karşı yüksek oranda dirençlidirler (Burggraaf ve Cot 1996). İnorganik membranlar, polimerik membranlara nazaran çok daha maliyetli olmalarına rağmen, yüksek sıcaklık değerlerinde uzun süreli dayanma gücü, ağır çevre koşullarına (kimyasal ayrışma, pH ve diğer koşullar gibi), yüksek basınca ve mikrobiyolojik bozunmalara karşı yüksek kararlılık ve direnç gösterme avantajlarına sahiptirler.
Günümüzde hala yüksek maliyet gerektirmeleri en büyük dezavantajıdır. Ayrıca kırılgan oluşları (özellikle yoğun paladyum membranlarda), modül hacmine oranla düşük membran yüzey alanına sahip olmaları, geniş çaplı mikro gözenekli membranlarda yüksek seçiciliği sağlamanın zorluğu ve yüksek kirlenme, tıkanma gibi dezavantajlara sahiptirler (Bonekamp 1996). Ancak ileride bu dezavantajlar giderilebilirse, birçok endüstri alanında verimli kullanılabilirler.
Seramik membranlar
Günümüzde, gözenekli seramik membranlar üretmek için çok çeşitli malzemeler kullanılmaktadır. Piyasadaki hemen hemen tüm membranları içeren gözenekli membranların çoğu, metal oksitlerden oluşur. Tercihen kullanılan oksitler; alüminyum oksit veya alümina (Al2O3), zirkonyum oksit veya zirkonya (ZrO2), titanyum oksit veya titanya (TiO2) ve silisyum oksit veya silika (SiO2) olarak verilebilir. Ayrıca, bu metal oksitlerin karışımları da sıkça kullanılmaktadır. Pervaporasyon ve gaz ayrım işlemleri için kullanılan mikro gözenekli membranlar arasından silikadan başka zeolit ve mikro gözenekli karbon isimli diğer metallerin de kullanılması uygun görülmüştür.
Yüksek geçirgenlik ve istenilen seçicilik değerlerinin elde edilmesi için piyasada bulunan tüm gözenekli seramik membranlar ve laboratuvar ortamında üretilen membranların çoğu asimetriktir. Bu durum, seramik membranın çok açık bir gözenek yapısına sahip destekten oluştuğu ve desteğin üstünde ise, daha küçük gözenekli bir veya daha fazla ince tabakanın yer aldığı anlamına gelir. En üst tabaka en küçük gözenekleri içerir ve gözenekli membranların gerçek seçiciliğini ifade eder. Destek, membrana mekanik güç sağlamak için kullanılır. Ara tabakalar ise membranın gözenek boyutunu ve yüzey pürüzlülüğünü kademeli olarak azaltmak için kullanılır.
Membran destek yapıları genel olarak slip-döküm ve ekstrüzyon yöntemleri ile elde edilir. Metal-oksit ara tabakaların ve üst katmanın hazırlanmasında kullanılan esas yöntem ise sol-jel tekniğidir. Mezo gözenekli ara tabakalar, kolloidal sollar ile hazırlanırken mikro gözenekli üst tabakalar ise polimerik sollar yardımıyla oluşur. Sollar, metal tuzları veya metal organik başlatıcılar (prekürsor) kullanılarak hazırlanır.
Katmanlar, daldırma-kaplama yöntemiyle seramik destekler üzerine veya bir önceki çok katmanlı yapı üzerine kaplanarak elde edilir. Desteğin veya bir önceki çok katmanlı yapının gözenekliliği solun jelleşmesine yol açar. Bu tabakalar daha sonra kurutulur ve son membran şeklini alabilmesi için ısıl işleme tabi tutulur. Uygulanan bu ısıl işlem, kalsinasyon veya sinterleme olarak adlandırılır ve amacı ise kuruyan tabakanın kristalografik ve morfolojik yapısını kararlı hale getirmektir. Hazırlanış yönteminden dolayı, tüm tabakalar polikristaldir ve aralarında gözenekler bulunan bir parçacık paketinden oluşur. Ara ve üst tabakaların parçacık büyüklüğü, sol-jel yöntemine ve kalsinasyon sıcaklığına bağlı olup bu durum gözenek boyutuyla ilişkilidir. Kalsinasyon/sinterleme nedeniyle, parçacıklar arasındaki temas noktaları ve daha uzun parçacık sınırlarını oluşturur.
Gözenekli seramik membranlar, esas olarak zorlu sıcaklık koşulları veya çözücüler ve asit ya da kostik çözeltiler gibi kimyasal maddelerin yer aldığı ultrafiltrasyon ve mikrofiltrasyon uygulamalarında kullanılır. Bu durumlarda, daha ucuz polimer membranların sınırlı bir kararlılığı vardır: genellikle sadece ⁓100 °C’nin altındaki sıcaklıklara dayanabilirler, birçok çözücüde ve güçlü asitlerde veya bazlarda şişer veya kısmen çözülürler. Buna karşılık seramik membranlar, genellikle yüksek kimyasal ve termal kararlılıkları ile bilinirler. Bu kararlılık, seramik membranla üretilen mikrofiltrasyon ve ultrafiltrasyon proseslerinin gıda, biyoteknoloji ve eczacılık gibi sektörlerde kullanımını cazip kılar.
Seramik membranlar gaz ayırma ve üretme proseslerinde de yaygın olarak kullanılır. Spesifik olarak, seramik membranlar, herhangi bir çözücü içinde şişmeye karşı duyarsızdır; kirlilikten kurtulmak için çok çeşitli temizlik maddelerine karşı oldukça dirençlidirler ve yüksek sıcaklıklarda sterilize edilebilirler.
Bununla birlikte, bazı çözülmesi gereken sorunları mevcuttur. Bunlar;
- Yüksek sıcaklıklarda aşırı hassasiyet
- Bazı türlerinde stabilizasyon eksikliği,
- Membran kırılma ve çatlamaları,
- Yüksek sıcaklıklarda son derece hassas seçicilik,
- Düşük sızdırmazlık olarak sıralanabilir.
Silika membranlar
Silika ve hibrit inorganik-organik silika membranlar, inorganik membranların sırasıyla dördüncü ve beşinci sınıfını temsil eder. Membranlar, genellikle bir makro gözenekli destek, bir veya daha fazla mezogözenekli ara katman ve geçirgen bir mikro gözenekli üst katmandan oluşur. Mikrogözenekli üst katmandaki gözenekler genellikle 2 nm’den daha küçüktür. Gaz ayrıştırması için bunların 0,7 nm’den az olması gerekir.
Mikrogözenekli silika membranlar, zeolitler gibi mekanik, termal ve kimyasal kararlılıkgösterirler. Kristalin zeolit membranların aksine, bu membranlar amorf silikadan oluşur.
Genel olarak, sol-jel ve kimyasal buhar birikimi (CVD) sentez yöntemleri kullanılarak gözenekli destekler üzerinde hazırlanırlar. Sol-jel yöntemi, seçiciliği ve geçirgenliği yüksek membranların üretilmesini sağlar. CVD ile hazırlanan membranlar, sol-jel yöntemleriyle hazırlanan membranlar için bulunan değerlere göre, gelişmiş seçicilik göstermektedir (Ockwig ve Nenoff 2007).
Sol-jel yöntemi ile elde edilen silika membranları, daha büyük kinetik çaplı gazlara (örneğin, CO2, N2 ve CH4) göre He, H2, H2O gibi gazlar için yüksek geçirgenlik değerigösterirler. H2/CO2, H2/N2, H2/CH4 ve CO2/CH4 seçicilikleri sırasıyla 98, >170, >5000 ve >100 kadar yüksek olabilir (de Vos ve Verweij 1998). Silika membranlar yüksek bir termal ve kimyasal kararlılık göstermelerine rağmen, yapılarında bulunan Si-OH gruplarıyla ilişkili olarak silika ağının bozulması nedeniyle su buharı içeren ortamlarda mükemmel performans özelliklerini kaybederler (Lu vd. 2007, Kanezashi ve Asaeda 2006, Uhlmann vd. 2009).
Zirkonyum veya titanyumdan hazırlanan mikro gözenekli membranlar, yüksek seçiciliğe yol açan amorf silikaya benzer sıkı ağ özellikleri göstermezler. Mikro gözenekli zirkonyum veya titanyum membranları için bildirilen değerler, mikro gözenekli silika için bildirilenden çok daha düşüktür (Van Gestel vd. 2006, 2008, Sekulic vd. 2004). Silika ağına, örneğin, NiO, CoO, MgO, Al2O3, ZrO2, TiO2, Fe2O3, Nb2O5 ve diğerleri gibi metal oksitler yüklenmiş ve böylece silika ağının modifikasyonu denenmiştir, ancak bu çalışmaların hiçbiri, başarılı olamamıştır veya nemli koşullar altında silika ağ yapısının kararlılığını ikna edici şekilde kanıtlamamıştır (Ockwig ve Nenoff 2007). Silika ağının hidrofobikliğini hedefleyen örneğin alkil veya florlanmış alkil gruplarının dahil edilmesiyle silika ağının modifikasyonu, mikro gözenekli silikanın hidrotermal kararlılığını önemli ölçüde geliştirmemiştir (de Vos vd. 1999, Wei vd. 2008).
Hibrit Organik-İnorganik silika membranlar
Bis-silil köprülü başlatıcı alkoksitlerden hazırlanan mikrogözenekli hibrit inorganik[1]organik silikamembranları, son birkaç yılda yoğun bir şekilde araştırılmıştır. Bunlar, ~150 °C’ye kadar olan sıcaklıklarda suyu, n-bütanol, propanol ve etanol gibi alkollerden ayıran pervaporasyon işleminde mükemmel performans göstermektedir (Castricum vd. 2008, Journal of Membrane Science, Castricum vd. 2011, Kreiter vd. 2009). 2010’dan beri hibrit silika membranlar piyasada bulunmaktadır.
Silika membranlarına benzer şekilde, hibrit silika membranları sol-jel yöntemleriyle hazırlanır. Organik köprüleme varlığı değişkenlik gösterebilir; bu, hem sentez parametreleri hem de malzeme ve membran özellikleri üzerinde büyük bir etkiye sahiptir (Kreiter vd. 2011). Pervaporasyon deneylerinde hidrotermal kararlılıklarının yanı sıra, hibrit silika membranlar, nitrik veya asetik asit tarafından kimyasal saldırılara karşı yüksek bir dirence sahiptir (Castricum vd. 2008, Journal of Material Chemistry, Kreiter vd. 2009).
Hibrit silika membranının önemli kararlılığı, silika ağının saf silikanınkinegöre daha fazla bağlana bilirliğinde köklenerek, nano ve mikro çatlak oluşumuna karşı dayanıklılık ve direnç gösterir (Castricum vd. 2011, Kreiter vd. 2011, Kanezashi vd. 2010, Journal of Membrane Science).
Ayrıca hibrit membranların gaz ayırımında uygulanması da incelenmiştir; H2/CO2 ve H2/CH4 ayrımındaki seçicilik, ticari uygulamalarını göz önüne almak için yetersiz görülmüştür (Kanezashi vd. 2009). Son zamanlarda, hibrit silika ağ yapısına metal veya geçiş metali oksitlerinin ilave edilmesi, hibrit membranların gaz ayırımında performansının arttırılması için bir strateji olarak kabul edilmiştir. Özellikle, niyobya (Nb2O5) gibi asidik oksitlerle yükleme yapmak, yüksek H2/CO2 seçiciliği elde etmek için umut verici bir yol gibi görünmektedir (Qi vd. 2010, 2011).
Makalenin devamına alt linkten ulaşabilirsiniz.
Yorum yap